для легкосплавных
бурильных труб
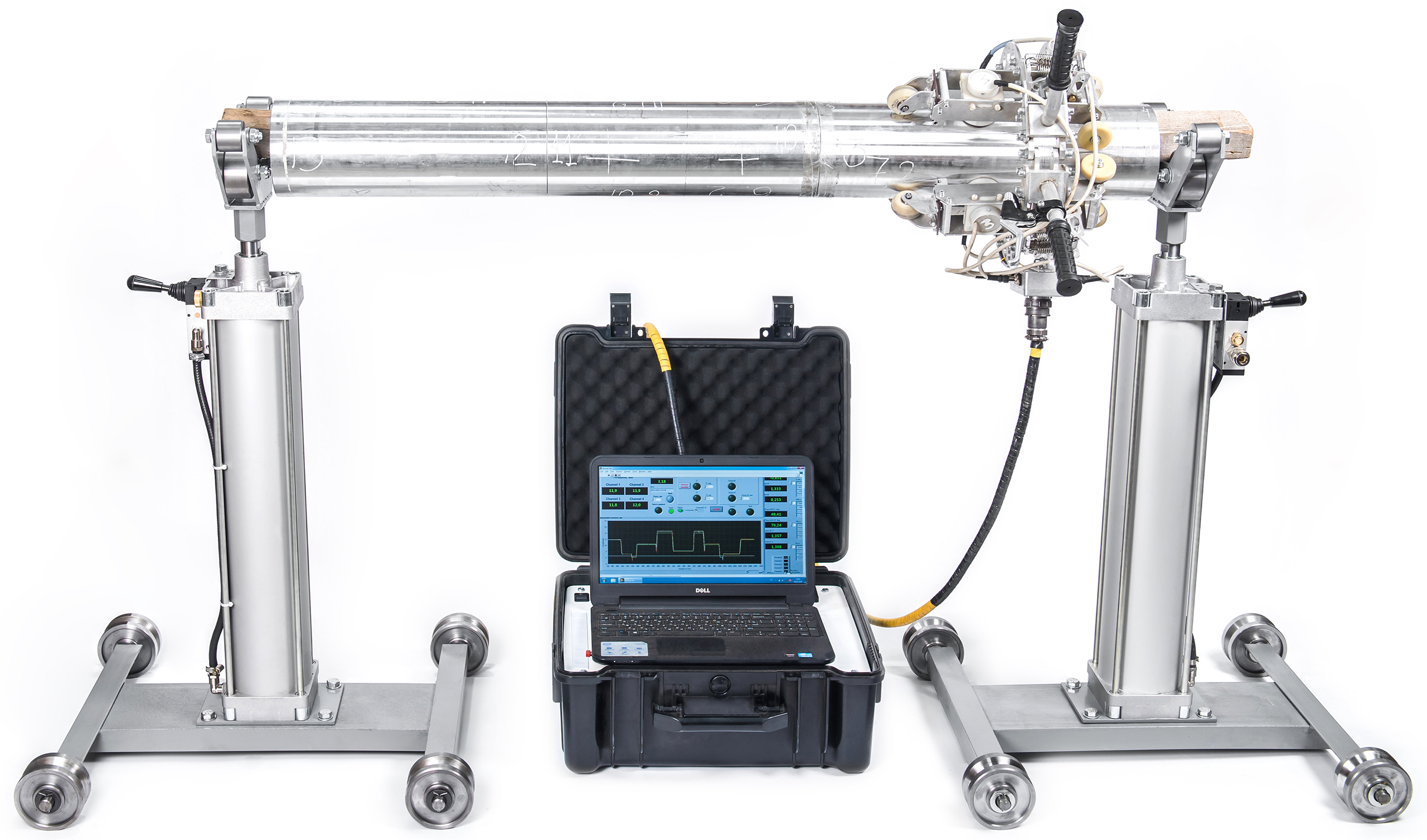
Рис. Общий вид комплекса
С каждым годом условия строительства скважин усложняются что, в свою очередь, повышает риск аварий, которые влекут за собой несчастные случаи с персоналом, наносят вред окружающей среде, приводят к простоям и значительным финансовым потерям.
Использование легкосплавных бурильных труб (ЛБТ) является одним из путей решения многих проблем бурения. Изготовленные из специальных лёгких, высокопрочных, коррозионностойких алюминиевых сплавов ЛБТ обладают рядом ценных физико-механических свойств, открывающих дополнительные возможности при бурении глубоких, горизонтальных скважин
Материал тела ЛБТ выполнен из сплавов, которые имеют более низкую, чем у сталей, твёрдость поверхности (в диапазоне 120-140 НВ), что говорит о несколько меньшей, чем у стальных труб стойкости к износу.
Прогрессирующий износ наружной поверхности опорных элементов бурильной трубы (замков, протектора и тела) в процессе бурения носит абразивный характер и обусловлен действием прижимающих усилий, приложенных к БК со стороны стенок скважины. Эти усилия зависят, в первую очередь, от веса бурильной трубы в буровом растворе, а также от осевой нагрузки на долото, центробежных сил при вращении БК, «баклинга» и других факторов. Абразивный износ наружных поверхностей распределяется по длине и периметру трубы неравномерно, причём максимальному износу, который носит, как правило, эксцентричный характер, подвергается средняя часть трубы.
Гидроабразивному износу подвержены внутренняя поверхность трубы и зоны, прилегающие к замковому соединению и внутренним высадкам труб, что объясняется некоторым сужением проходного сечения и турбулизацией потока промывочной жидкости. Особенно интенсивно этот процесс происходит при использовании промывочных жидкостей с повышенным значением твёрдой фазы и растворов, обработанных твёрдыми утяжелителями.
Таким образом, использование ЛБТ ставит важную задачу инспекции труб во время эксплуатации, при окончании бурения и при повторном использовании в составе БК. Существующие методы инспекции предусматривают неразрушающий контроль замков ЛБТ (визуальный и измерительный, ультразвуковой, магнитопорошковый методы), которые позволяют достаточно хорошо оценить состояние и возможность дальнейшего использования этих элементов бурильной трубы. Инспекция тела трубы предусматривает визуальный и измерительный контроль и ультразвуковую толщинометрию тела трубы в 3-х сечениях по длине и в 4-х точках в каждом сечении.
Этого явно недостаточно для полной оценки состояния тела трубы: возможны локальные язвы на внутренней поверхности трубы, локальные утонения стенки, задиры и другие дефекты, не выявляемые визуально и вероятность обнаружения которых толщинометрией в небольшом количестве точек крайне мала.
Мы предлагаем дополнить стандартную инспекцию трубы сплошным контролем тела трубы с использованием специальной установки, основанной на вихретоковом методе контроля. Такая процедура аналогична процедуре электромагнитного контроля, используемой для инспекции стальных бурильных труб по стандарту DS-1 (кат.3-5).
Работа нашей установки основана на возбуждении в теле ЛБТ вихревых токов и их регистрации с помощью специальных датчиков. Сигнал, снимаемый с датчика, будет зависеть от количества металла под датчиком (т.е. в нашем случае от толщины стенки трубы), от электропроводности материала трубы (марки алюминиевого сплава), расстояния от датчика до поверхности трубы, от локальных повреждений поверхности трубы под датчиком. Таким образом, метод позволяет классифицировать трубы по материалу, из которого они изготовлены, определять остаточную толщину стенки трубы, выявлять локальные утонения стенки из-за неравномерного износа, выявлять трещины и задиры на поверхности трубы, а в случае достаточно больших трещин и на внутренней поверхности. Метод является бесконтактным и не предъявляет жестких требований к очистке поверхности контролируемой трубы.
Установка состоит из каретки с вихретоковыми датчиками (рис.1), которая устанавливается на исследуемую трубу и перемещается по ней, блока электроники и персонального компьютера.
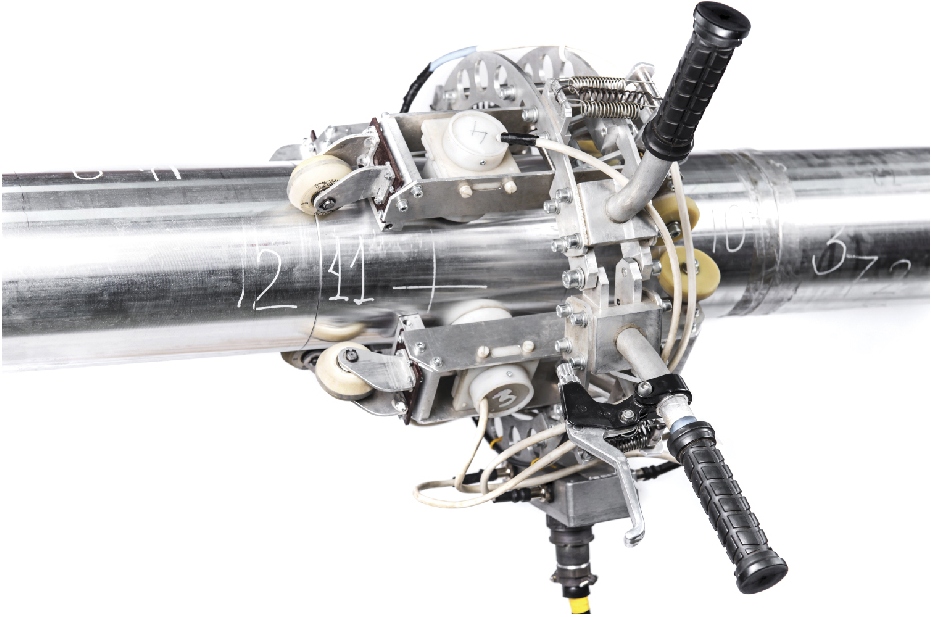
Рис. 1. Каретка с датчиками.
Каретка представляет собой тележку, которая легко устанавливается на трубу и легко снимается. На тележке укреплена конструкция, на которой по окружности размещены вихретоковые датчики. Количество датчиков (от 4 до 8) и их диаметры таковы, что позволяют контролировать практически всю поверхность трубы в данном сечении. Каретка в свою очередь перемещается вдоль трубы, позволяя проводить контроль по всей поверхности трубы. Вихретоковые датчики с помощью кабелей соединены с блоком электроники.
Блок электроники предназначен для генерации синусоидального напряжения для вихретоковых датчиков, приема, усиления и обработки сигналов с датчиков. Усиленный и сформированный сигнал преобразуется в цифровую форму и передается для дальнейшей обработки в персональный компьютер.
Пример показаний прибора приведен на рисунке 2, на котором показана виртуальная панель прибора на экране персонального компьютера. В верхней левой части экрана приведены показания текущей толщины стенки трубы измеренной каждым из датчиков. Правее показано текущее расстояние от датчиков до поверхности трубы (зазор). Диаграмма, расположенная ниже, представляет собой протокол измерений толщины стенки конкретного образца трубы. В данном случае контролировался контрольный образец (рис. 3), представляющий собой отрезки ЛБТ 147 с толщинами стенки 12, 7, 6, 10, 14 и 8 мм. Отрезки 12 и 7 мм, 6 и 10 мм, 14 и 8 мм жестко неразъемно соединены между собой без зазоров. Три образца помещены на непроводящий стержень образуя один образец. Между отрезками существует небольшой зазор (0,1 – 0,2 мм). На диаграмме показания каждого из датчиков представлены в виде линий различного цвета. Белая линия показывает браковочный уровень по толщине (в нашем случае 6 мм). Браковочный уровень может быть программно изменен. На диаграмме четко прослеживается переход каретки от образца одной толщины стенки к другой. При переходе для жестко соединенных образцов показания прибора меняются плавно, а в случае наличия механического зазора (с точки зрения прибора это наличие трещины в трубе) показания меняются резко с наличием провалов.
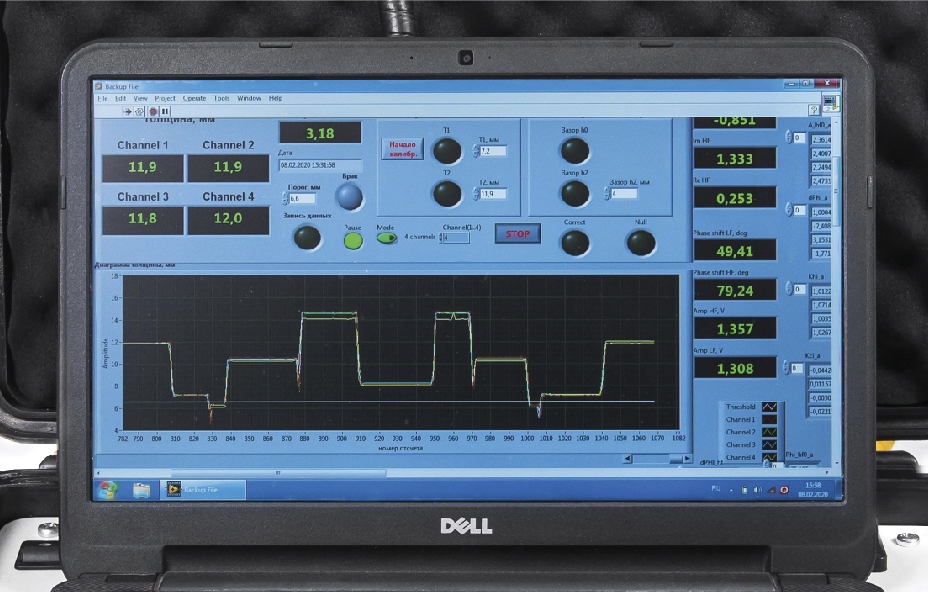
Рис.2. Протокол измерения контрольного образца
Лабораторные и полевые испытания прибора показали, что в диапазоне измеряемых толщин стенки трубы 7 – 12 мм и зазоре 0 – 6 мм точность измерения толщины стенки трубы составляет 0.2 мм. Во всем диапазоне измерений (5 -16 мм и зазор до 12 мм) точность измерений составляет не хуже 0.5 мм(на больших толщинах). Прибор уверенно различает трубы, изготовленные из материалов с электропроводностью отличающейся на 2-3 %.
Измерения на образцах с искусственными дефектами в виде пропилов разной длины и раскрытия, показали, что прибор уверенно фиксирует дефекты длиной сравнимой с диаметром датчика (30 – 40 мм) и раскрытием от 1 мм.
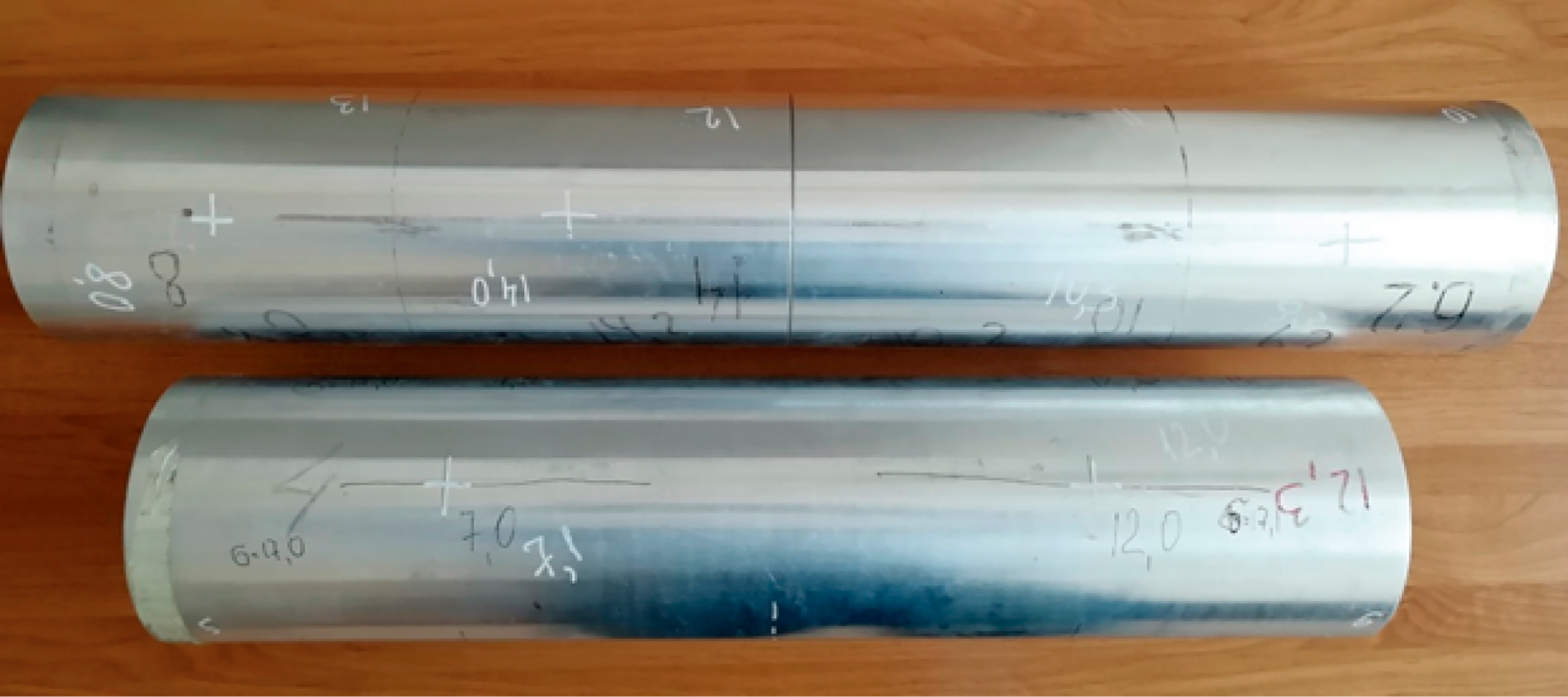
Рис.3. Контрольный образец
Прибор реализован в переносном варианте, может быть легко транспортирован на место проведения инспекции. Результаты измерений представляются на экране компьютера в виде диаграмм и документируются в файл, который затем может быть автономно просмотрен.